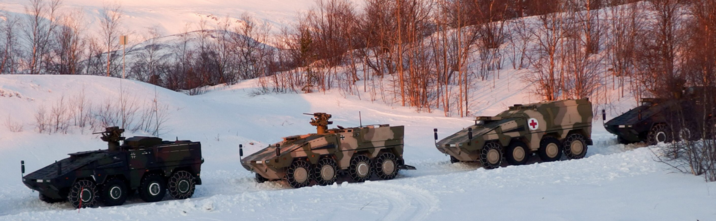
Full innovative power with increasing braking force
What began in 1997 with the development of the prototype continues to this day: the development of all brakes installed in the 8x8 BOXER. In close cooperation with Krauss-Maffei Wegmann (KMW) and Rheinmetall, an absolutely successful model has been created whose requirements are constantly growing. And this is precisely where KNOTT, the specialist for custom brake solutions from Eggstätt, comes into its own. In research, development and not least in targeted customisation.
"When we started developing the brake for the BOXER in 1997, I was still a very young design engineer," says Richard Hamberger, now Head of Sales at KNOTT. He himself played a major role in developing the prototype back then. Even 22 years ago, the requirements were rightly high. Because, of course, a brake for military use has to be prepared for everything: the greatest possible protection against dirt and moisture, extremely good braking power on any terrain - and, of course, maximum reliability. Not only when braking itself, but above all when releasing the brake.
"At that time, everything was still designed for use in the actual programme nations of Germany, the Netherlands and Great Britain. In other words, for central or northern European conditions," adds Hamberger. "This area has now expanded significantly."
Multifunctional vehicle in multinational operation
Due to its modular design - drive module and mission module - the BOXER is designed for a wide range of applications.
Whether troop carrier, load transporter, command vehicle or ambulance: KNOTT has developed the optimum solution here together with its partners KMW and Rheinmetall.
Axles one to three are braked by the hydraulic HFS 4x85 fixed calliper disc brake, while a hydraulic HFS 2x85 fixed calliper disc brake is installed in the fourth axle. Both have a brake disc diameter of an impressive 510 mm and 4 or 2 pistons with a diameter of 85 mm each.
In addition, there is the parking brake system located on the transfer case, which consists of two FSG 110 hydraulic spring-loaded sliding caliper brakes with a common brake carrier. Including the compressed air-hydraulic pressure converter for actuation, which also comes from KNOTT. And all these brakes have plenty to do.
"At the beginning of development, the brakes were still designed for a permissible total weight of the Boxer of 31 to 33 tons," explains Franz Schweiger, Head of Design at KNOTT. "As a result of ever more technical improvements, new requirements for passive protection such as armor plating and a wide variety of loadings, we are now talking about just under 40 tons that need to be braked."
And which are being slowed down. No longer just in Europe, but soon also in Australia. Because the nation on the other side of the world has also decided to integrate the BOXER into the force.
New specifications, new test benches, familiar reliability
With the deployment and export of the BOXER came not only new challenges in terms of heat and cold resistance. The test requirements for the approval of a brake are also different. In order to meet the latter in particular, KNOTT has developed and built a new test stand that really does meet all eventualities.
"Here on site, we are able to realistically simulate braking from 100 km/h, for example. One of the reasons we know this so well is because our results on the test bench were comparable to those on the DEKRA test track," Schweiger is pleased to say, adding that tests of up to 70,000 Nm are possible on the KNOTT test bench.
Since the BOXER is running so successfully, further Missons modules are now being planned, which will probably not put any less weight on the driving module. The latest version of the BOXER brakes is already set up for this. Higher friction values and higher thermal resistance are of course mandatory here - as well as a new wear indicator of the already maintenance-friendly brake system helps to minimise possible downtimes. This is made possible, among other things, by the special high-performance brake lining, which is also an in-house development of the KNOTT Group.
KNOTT: Experience, commitment - and on site worldwide!
Thanks to decades of experience in the field of braking systems for military and other special vehicles (e.g. dump trucks, agriculture and much more), KNOTT not only has the necessary know-how. The company's core competencies also include the ability to manufacture prototypes in-house as well as series production, even of small and medium quantities.
"And we are also no strangers to the term 'local content' - in other words, adding value in the customer's own country," adds Hamberger. "Rather, with our worldwide subsidiaries and partnerships, we are always pleased to be able to be directly on site."
The promise "We make your brake!" is clearly a maxim lived out at KNOTT. To find out more, feel free to contact our application engineering department directly: